Custom medical implants have undergone a revolution thanks to the combination of CAD, simulation, and 3D printing technology, raising the bar for individualized healthcare. A groundbreaking partnership between PTC, Hexagon, and Tel Aviv Medical Center illustrates how these cutting-edge technologies can address complex medical challenges. At the heart of this endeavor lies the creation of a fully customized scapula implant for a young cancer patient, showcasing the transformative potential of digital tools in medicine.
The Purpose of Modern Digital Tools
Creo Design CAD Software from PTC
The bespoke scapula implant was designed primarily using PTC’s Creo Design CAD software. This tool enabled precise simulation of the implant, considering the patient’s unique anatomical features. By utilizing imaging data from CT and MRI scans, the software generated a highly detailed 3D model, which served as the blueprint for subsequent manufacturing steps.
Simufact Additive Simulation by Hexagon
Hexagon’s Simufact Additive software was employed to simulate the additive manufacturing process. This ensured that potential issues, such as thermomechanical distortions during 3D printing, were identified and resolved before production began. This process enhanced the implant’s structural integrity while reducing material waste.
VGSTUDIO MAX for Quality Verification
VGSTUDIO MAX was used to process CT scan data and verify the quality of the printed implant. This tool was crucial in ensuring the final product met stringent engineering and medical standards, validating it for surgical use.
A Customized Approach to a Challenging Problem
The young patient, diagnosed with a rare and aggressive form of cancer, faced severe damage to the scapula and surrounding muscles. Traditional treatment options would have significantly impaired shoulder functionality. However, leveraging advanced digital tools, the team developed a titanium scapula implant tailored precisely to the patient’s anatomy. This innovative solution not only preserved mobility but also set a benchmark for addressing similar cases in the future.
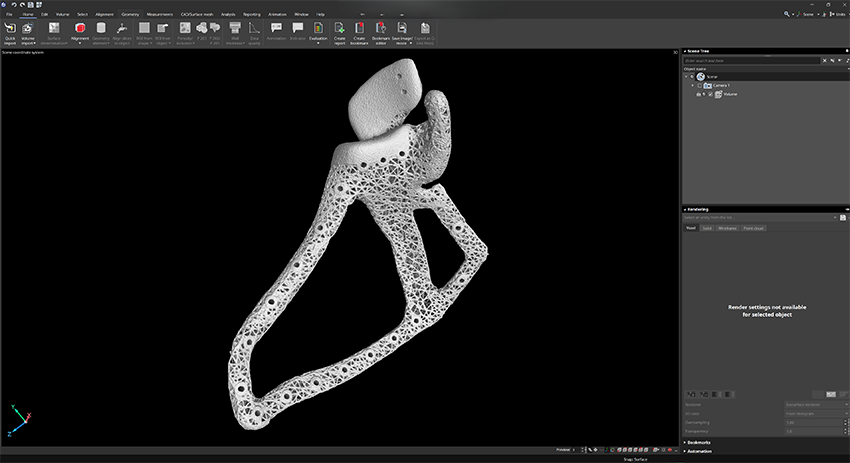
Key Design Challenges
The design process involved overcoming several challenges, including:
- Preserving the scapula’s kinematics and anatomical volume.
- Minimizing implant weight while optimizing mechanical properties.
- Ensuring accurate muscle attachment anchorage points.
- Incorporating lattice structures to promote tissue and muscle growth.
- Verifying implant durability for arm and shoulder movements using mechanical models.
- Reducing print iterations and ensuring manufacturability through simulation tools.
Multidisciplinary Collaboration: A New Era in Medicine
The success of this project underscores the critical importance of multidisciplinary collaboration. Engineers, surgeons, and software developers worked in close coordination to ensure the implant met both technical and medical requirements. Beyond benefiting the patient, this collaboration has paved the way for further advancements in personalized medicine.
Implications for the Medical Industry
This innovation highlights the transformative potential of CAD, simulation, and 3D printing in medical applications. These tools enable the creation of implants that integrate seamlessly with a patient’s anatomy, enhance tissue regeneration, and extend implant lifespan. Such advancements are revolutionizing patient care and surgical techniques.
Expanding the Horizons of Personalized Medicine
The future of medicine holds immense potential for integrating advanced digital technologies. Innovations such as bioactive implants, which intelligently interact with the human body, are reshaping the landscape. These implants not only restore damaged structures but actively support healing by promoting tissue regeneration and ensuring long-term compatibility.
Exciting Developments Ahead
Future innovations may include implants with embedded sensors to monitor healing in real-time. Further refinement of lattice structures could enhance integration with adjacent tissues, accelerating recovery and improving outcomes. With ongoing research and collaboration, the potential for innovation remains boundless.
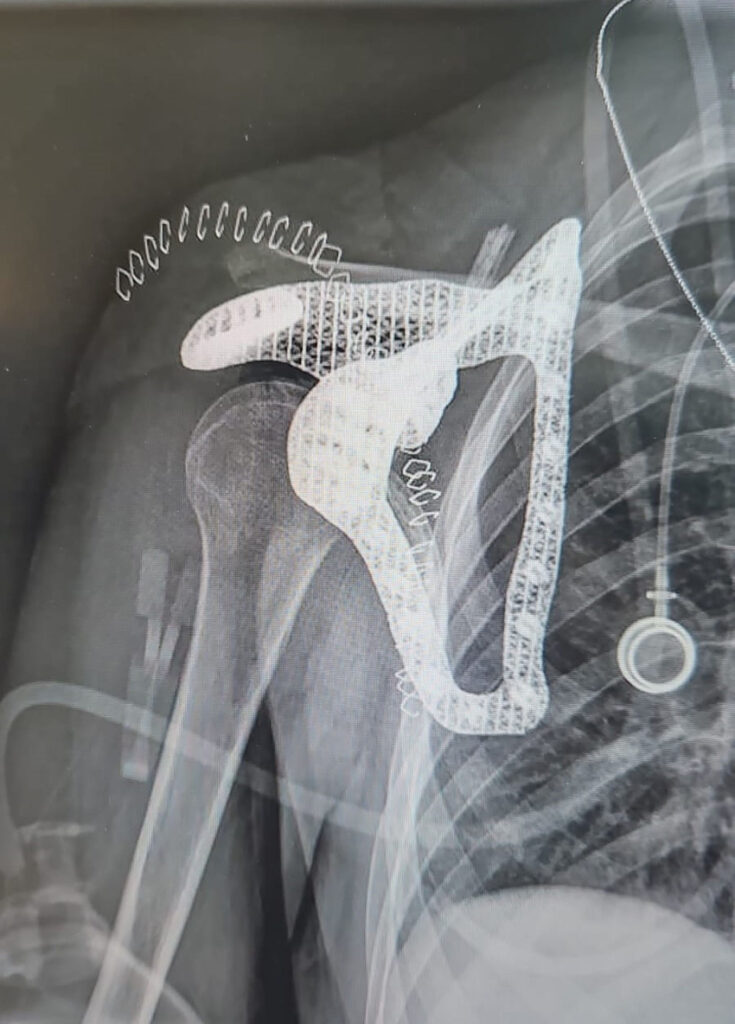
The Future of Custom Medical Implants
The success of this customized scapula implant exemplifies how technology is redefining healthcare. As CAD, simulation, and 3D printing technologies continue to evolve, they will offer novel solutions to previously insurmountable challenges. This case serves as an inspiring example of what can be achieved when expertise from diverse fields converges to tackle complex problems.
The Patient’s Journey: An Inspirational Story
From diagnosis to recovery, the patient’s journey has been nothing short of extraordinary. The swift restoration of mobility and quality of life underscores the profound impact of personalized medical care. This success story offers hope to others facing similar challenges.
Wrapping Up
The collaboration between Hexagon, PTC, and Tel Aviv Medical Center marks a significant milestone in personalized medicine. By harnessing the power of CAD, simulation, and 3D printing technologies, the team transformed a young cancer patient’s life while setting a new standard for medical innovation. The integration of these technologies heralds a new era in healthcare, promising even greater possibilities for the future.